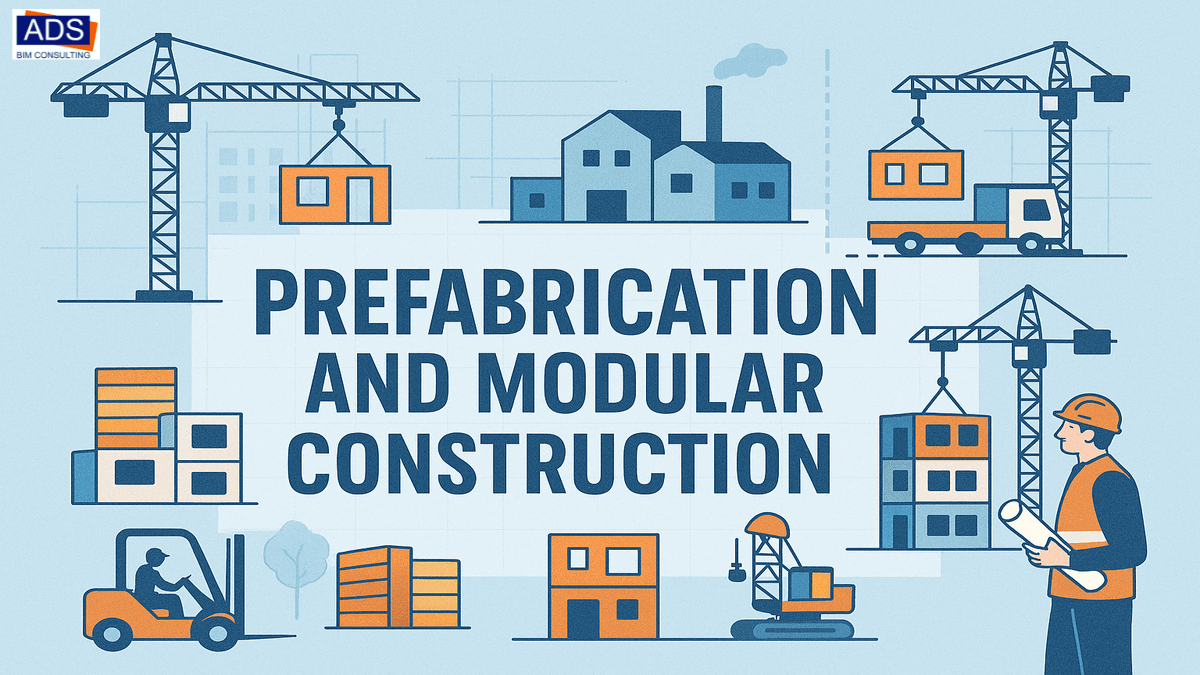
Prefabrication and Modular Construction: The Future of Smart, Sustainable Building
In today’s fast-paced construction landscape, Prefabrication and Modular Construction are revolutionizing how buildings are planned, designed, and delivered. These advanced methodologies are not just a trend—they’re shaping the future of construction with unmatched efficiency, sustainability, and cost-effectiveness.
Whether you’re a real estate developer, architect, contractor, or facility manager, understanding the power of prefabrication and modular construction can give you a strategic edge.
What is Prefabrication and Modular Construction?
Prefabrication refers to the process of manufacturing building components off-site in a controlled environment and then transporting them to the construction site for assembly.
Modular Construction is a form of prefabrication where entire sections (or modules) of a building are constructed off-site and then assembled on-site like building blocks.
Together, these approaches offer faster timelines, less waste, improved quality control, and greater design flexibility compared to traditional construction.
Why Prefabrication and Modular Construction are Gaining Popularity
- Faster Project Timelines
Construction schedules are cut by up to 50% with off-site fabrication and parallel on-site work.
- Cost Savings
Reduced labour costs, fewer delays, and minimized material waste contribute to significant budget savings.
- Sustainability Benefits
Controlled factory environments reduce waste, energy usage, and environmental impact.
- Consistent Quality
Standardized processes and automated machinery ensure higher precision and fewer reworks.
- Safer Working Conditions
Prefabricated systems lower on-site activity, reducing safety risks and accidents.
Real-Life Use Cases of Prefabrication and Modular Construction
- Healthcare Facilities: Modular construction enabled rapid delivery of COVID-19 testing and treatment centres globally.
- Hospitality & Hotels: Marriott and Hilton have built hundreds of modular hotels with reduced construction time.
- Multifamily Housing: Developers use prefabrication for apartments and condos to speed up occupancy and ROI.
BIM Integration with Modular Construction
Building Information Modeling (BIM) plays a critical role in optimizing prefabrication. At ADS BIM, our BIM services support modular construction through:
- Clash Detection before fabrication
- 4D simulation for timeline optimization
- Digital prefabrication and coordination
➡️ Learn more about our BIM for Construction Services and how we support modular project success.
Stats That Prove the Shift
- 82% of general contractors plan to increase prefabrication use in the next 3 years.
- 90% of modular projects are delivered on time vs. only 40% in traditional construction.
- Modular construction is expected to be a $157 billion industry by 2032.
Future Trends in Prefabrication & Modular Construction
- 3D Printing + Modular: Emerging 3D printed modules are transforming small housing units.
- Green Materials: Focus on sustainable prefabricated materials like bamboo and recycled steel.
- AI + Robotics: Automation is being used for precision cutting, assembling, and quality checks.
- 4D and 5D BIM for Construction Planning
- Scan to BIM: Revolutionizing Renovation Projects
- Construction Documentation with BIM
Prefabrication and Modular Construction are no longer “alternative” methods—they are becoming mainstream for their ability to deliver projects faster, greener, and smarter. Embracing these technologies is crucial for construction professionals aiming to stay competitive.
👉 Ready to integrate prefabrication and modular strategies into your next project?
Let our BIM experts help you plan and execute with precision.
📩 Contact us now at info@adsbim.com
🌐 Visit: www.adsbim.com
Frequently Asked Questions (FAQ)
Q1: How does modular construction differ from traditional construction?
A: Traditional construction builds everything on-site, while modular construction assembles pre-built modules manufactured off-site, significantly reducing time and improving quality.
Q2: Is modular construction only suitable for residential buildings?
A: No, it’s widely used in commercial, healthcare, hospitality, and educational facilities.
Q3: What’s the role of BIM in prefabrication?
A: BIM enhances accuracy, coordinates design, detects clashes early, and simulates construction sequences, making prefabrication smoother and more reliable.
Q4: Are prefabricated buildings less durable?
A: Not at all. Prefabricated buildings often meet or exceed the durability of traditional ones due to stringent factory-level quality controls.
Q5: How can I start implementing modular construction?
A: Begin with a feasibility analysis and partner with BIM consultants like ADS BIM who specialize in modular-ready project planning and coordination.
#Prefabrication #ModularConstruction #BIM #SmartConstruction #SustainableConstruction #ConstructionInnovation #OffsiteConstruction #ModularBuilding #4DBIM #5DBIM #ADSbim